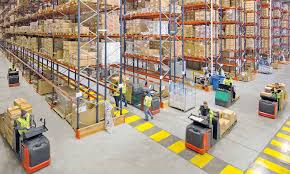
Seasonal inventory fluctuations present unique challenges for warehouse managers, requiring strategic planning and efficient execution to maintain optimal operations. Demand spikes during peak seasons can lead to storage constraints, order fulfillment delays, and increased labor costs. Conversely, off-peak periods may result in excess inventory and underutilized resources. Implementing proactive inventory management strategies ensures that warehouses can efficiently handle these fluctuations while maintaining productivity and profitability.
Analyzing Seasonal Demand Trends
Understanding historical demand patterns is crucial for preparing a warehouse for seasonal inventory changes. Analyzing sales data, market trends, and customer purchasing behavior helps forecast demand more accurately. Key strategies include:
- Reviewing historical order data to identify peak seasons and slow periods.
- Using predictive analytics to anticipate future demand fluctuations.
- Collaborating with suppliers and retailers to align inventory levels with expected demand.
Accurate forecasting allows warehouses to adjust stock levels, staffing, and logistics to meet seasonal demands effectively.
Optimizing Warehouse Layout and Storage
A well-organized warehouse layout is essential for accommodating seasonal inventory fluctuations. Maximizing storage space and improving accessibility can enhance efficiency during peak seasons. Some key strategies include:
- Adjustable racking systems: Implementing modular or dynamic shelving allows for flexible storage configurations.
- Temporary storage solutions: Renting additional warehouse space or using temporary storage units can help manage excess inventory.
- Reorganizing pick paths: Optimizing picking routes ensures faster fulfillment during high-demand periods.
Properly structuring the warehouse layout reduces congestion, improves workflow, and enhances order fulfillment speed.
Streamlining Inventory Management Practices
Implementing efficient inventory management techniques ensures that warehouses can quickly adapt to fluctuating inventory levels. Key best practices include:
- Just-in-time (JIT) inventory: Reducing excess stock by receiving goods as needed minimizes storage costs and waste.
- FIFO and LIFO methods: Using First-In, First-Out (FIFO) or Last-In, First-Out (LIFO) strategies ensures that perishable or seasonal products are managed efficiently.
- Regular cycle counts: Conducting frequent inventory audits helps maintain accurate stock levels and prevents shortages or overstocking.
Using an advanced warehouse management system (WMS) can further enhance inventory tracking and accuracy during seasonal peaks.
Leveraging Technology for Efficiency
Automation and digital solutions play a vital role in managing seasonal inventory changes. Investing in technology can optimize warehouse operations and improve overall efficiency. Some key technologies include:
- Automated storage and retrieval systems (AS/RS): These systems enhance inventory handling and reduce manual labor.
- RFID and barcode scanning: Implementing scanning technologies ensures real-time inventory tracking and reduces errors.
- AI-driven demand forecasting: Machine learning algorithms help predict seasonal trends with higher accuracy.
Additionally, palletizing strategies can help streamline warehouse operations by optimizing how goods are stored and transported. Efficient palletizing reduces space constraints, speeds up order fulfillment, and minimizes damage during handling.
Scaling Workforce and Operations
Managing seasonal inventory fluctuations requires a flexible workforce strategy. Increasing labor capacity during peak seasons ensures timely order fulfillment without overwhelming permanent staff. Effective workforce management practices include:
- Hiring temporary staff: Bringing in seasonal workers helps manage increased order volumes.
- Cross-training employees: Training permanent staff in multiple roles increases adaptability and reduces bottlenecks.
- Using labor management systems: Workforce planning tools help allocate resources efficiently and optimize shifts.
A scalable workforce strategy ensures that warehouse operations remain efficient, even during demand surges.
Enhancing Supplier and Logistics Coordination
Strong coordination with suppliers and logistics partners is crucial for managing seasonal inventory changes effectively. Proactive communication helps prevent supply chain disruptions and ensures timely replenishment. Best practices include:
- Establishing flexible supplier agreements to accommodate changing order volumes.
- Optimizing inbound and outbound logistics to minimize delays and bottlenecks.
- Implementing contingency plans for unexpected supply chain disruptions.
By strengthening supplier and logistics coordination, warehouses can ensure seamless inventory flow during peak and off-peak seasons.
Conclusion
Managing seasonal inventory fluctuations in warehouses requires a combination of data-driven forecasting, optimized storage solutions, efficient workforce planning, and strategic supplier coordination. By leveraging technology, implementing scalable solutions, and optimizing warehouse layout, managers can ensure smooth operations throughout the year. Additionally, using palletizing techniques can further improve warehouse efficiency by streamlining storage and transportation processes. With the right strategies in place, warehouses can maintain high productivity levels, reduce costs, and enhance customer satisfaction, regardless of seasonal demand changes.